-
Çelik Raylı Tekerlekler
-
Demiryolu Tekerlek Seti
-
Tren Ray Tekerlekleri
-
Alüminyum Alaşımlı Jantlar
-
Demiryolu yedek parçaları
-
Elastik Ray Klipsi
-
Demiryolu araçları
-
Raylı Tekerlek Aksı
-
Çelik Raylı Ray
-
Demiryolu Balık Tabakları
-
Demiryolu Lastikleri
-
Hassas Dövme Parçaları
-
Yatırım Döküm Parçaları
-
Demiryolu Ray Bağlantı Elemanları
-
Demiryolu Parça Arabaları
-
Raylı Ray Ölçüm Ekipmanları
Paslanmaz Çelik Yatırım Döküm Parçaları Metal Damgalama OEM
Menşe yeri | Çin |
---|---|
Marka adı | Kingrail |
Sertifika | ISO |
Model numarası | hassas döküm |
Min sipariş miktarı | Pazarlık edilebilir |
Fiyat | negotiable |
Ambalaj bilgileri | standart ihracat paketi veya müşteri isteğine göre |
Teslim süresi | 1-30 iş günü |
Ödeme koşulları | L/C, D/A, D/P, T/T, Western Union, MoneyGram |
Yetenek temini | 1000000ton |
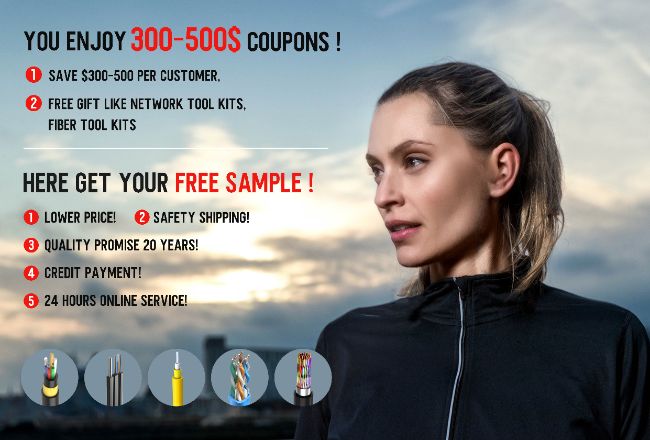
Ücretsiz numuneler ve kuponlar için bana ulaşın.
Naber:0086 18588475571
wechat: 0086 18588475571
Skype: sales10@aixton.com
Eğer herhangi bir endişeniz varsa, 24 saat online yardım sağlıyoruz.
xMalzeme | Paslanmaz çelik, Karbon çeliği, Alaşımlı çelik | Şartname | özelleştirilmiş |
---|---|---|---|
Ürün adı | Döküm Damgalama parçaları | Başvuru | Sanayi Makinaları, Otomotiv, Elektrik |
İşlem | yatırım dökümleri | Yüzey İşlem | Çinko kaplama, Boyama, Toz Boya, Elektro parlatma |
Test tesisleri | Spektrometre, CMM, Kaliperler, mikrometre, projektör Yükü | ||
Vurgulamak | Damgalama Paslanmaz Çelik Yatırım Döküm Parçaları,OEM Paslanmaz Çelik Yatırım Döküm Parçaları |
Paslanmaz Çelik Yatırım Döküm Parçaları Metal Damgalama OEM
Dökümlerin teorik sıvı metal şekillendirmesine genellikle döküm denir ve döküm şekillendirme teknolojisinin uzun bir geçmişi vardır.5.000 yıldan daha uzun bir süre önce atalarımız bakır ve bronz ürünler yapabildiler.Döküm, en yaygın kullanılan metal sıvı şekillendirme işlemidir.Sıvı metalin kalıp boşluğuna dökülmesi yöntemidir ve soğuduktan ve katılaştıktan sonra bir boşluk veya belirli bir şekle sahip bir parça elde edilir.
Sıvı kalıplar, makine ve ekipmanın büyük bir bölümünü oluşturur.Takım tezgahlarında, içten yanmalı motorlarda, madencilik makinelerinde ve ağır makinelerde toplam ağırlığın %70 ila %90'ını sıvı kalıplar oluşturur;otomobil ve traktörlerde %50 ila %70;Tarım makineleri %40 ila %70 arasında bir paya sahiptir.Aşağıdaki avantajlara sahip olduğu için sıvı şekillendirme işlemi çok yaygın olarak kullanılabilir:
(1) Karmaşık iç boşluk ve şekle sahip boşluklar üretebilir.Çeşitli kutular, makine yatağı, silindir bloğu, silindir kapağı vb.
(2) Süreç büyük bir esnekliğe ve geniş bir uyarlanabilirliğe sahiptir.Sıvı kalıplamanın boyutu neredeyse sınırsızdır ve ağırlığı birkaç gramdan birkaç yüz tona kadar değişebilir ve duvar kalınlığı 0,5 mm ila 1 m arasında değişebilir.Endüstride eritilerek sıvı haline getirilebilen herhangi bir metal malzeme sıvı kalıplama için kullanılabilir.Çok sünek dökme demir için, bir işlenmemiş parça veya parça üretmenin tek yolu sıvı şekillendirmedir.
(3) Sıvı kalıplama parçalarının maliyeti daha düşüktür.Sıvı kalıplama, atık parçaları ve talaşları doğrudan kullanabilir ve ekipman maliyeti düşüktür.Aynı zamanda, sıvı oluşturan parçaların işleme payı küçüktür, bu da metalden tasarruf sağlar.
Dökümler, çeşitli döküm yöntemleriyle elde edilen metal şekillendirici nesnelerdir, yani eritilmiş sıvı metal, önceden hazırlanmış döküm kalıbına dökme, enjeksiyon, emme veya diğer döküm yöntemleriyle ve soğutmadan sonra, öğütme ve sonraki diğer işleme yöntemleriyle enjekte edilir., belirli şekil, boyut ve özelliklerin ortaya çıkan nesnesi.
Dökümler için birçok sınıflandırma yöntemi vardır: kullanılan farklı metal malzemelere göre çelik dökümler, demir dökümler, bakır dökümler, alüminyum dökümler, magnezyum dökümler, çinko dökümler, titanyum dökümler vb. kimyasal bileşimine veya metalografik yapısına göre de farklı tiplere ayrılır.Örneğin, demir dökümler gri demir dökümler, sfero dökümler, vermiküler demir dökümler, dövülebilir demir dökümler, alaşımlı demir dökümler, vb. olarak ayrılabilir;farklı döküm yöntemlerine göre, dökümler sıradan kum dökümler, metal dökümler, kalıp dökümler, santrifüj dökümler, sürekli dökümler, hassas dökümler, seramik dökümler, elektro cüruf yeniden ergitme dökümleri, bimetal dökümler vb. En yaygın olarak kullanılan, tüm dökümlerin yaklaşık %80'ini oluşturan.Alüminyum, magnezyum, çinko ve diğer demir dışı metal dökümler çoğunlukla kalıp dökümleridir.
verim
Bununla birlikte, sıvı metal şekillendirme için birçok işlem vardır ve tam olarak kontrol edilmesi zordur, bu nedenle dökümlerin kalitesi yeterince kararlı değildir.Aynı malzemenin dövme parçalarıyla karşılaştırıldığında, sıvı oluşumunun gevşek yapısı ve kaba taneleri nedeniyle, büzülme boşlukları, büzülme gözenekliliği ve gözenekler gibi kusurlar içeride kolayca oluşur.Mekanik özellikleri düşüktür.Ayrıca emek yoğunluğu yüksek ve koşullar kötü.Mükemmel mekanik ve fiziksel özelliklere sahiptir.Mukavemet, sertlik ve tokluğun çeşitli kapsamlı özelliklerine sahip olabilir ve ayrıca aşınma direnci, yüksek sıcaklık ve düşük sıcaklık direnci, korozyon direnci vb. gibi bir veya daha fazla özel özelliğe sahip olabilir.
Dökümlerin ağırlık ve boyut aralığı çok geniştir.En hafif ağırlık sadece birkaç gramdır, en ağır 400 tona ulaşabilir, en ince duvar kalınlığı sadece 0,5 mm'dir, en kalın 1 metreyi geçebilir ve uzunluk birkaç milimetreden on metreye kadar olabilir.Farklı endüstriyel sektörlerin kullanım gereksinimlerini karşılayabilir.
kullanmak
Dökümler yaygın olarak kullanılmaktadır ve donanıma ve tüm mekanik ve elektronik endüstrilerine uygulanmaktadır ve kullanımları genişleyen bir trend haline gelmektedir.Özel olarak kullanılan inşaat, donanım, ekipman, inşaat makineleri ve diğer büyük makineler, takım tezgahları, gemiler, havacılık, otomobiller, lokomotifler, elektronik, bilgisayarlar, elektrikli ev aletleri, dökme işlemi
Takım tezgahı yatak dökümlerinin döküm işleminde, döküm sırasında yüksek sıcaklıkta döküm ve düşük sıcaklıkta döküm prensibi izlenmelidir.Erimiş metal sıcaklığının yükseltilmesi, kalıntıların tamamen erimesine ve cürufun yüzdürülmesine elverişli olduğundan, cüruf temizleme ve gazdan arındırma için uygundur ve takım tezgahı dökümlerinin cüruf içerme ve gözenek kusurlarını azaltır;daha düşük bir dökme sıcaklığı kullanmak, erimiş metaldeki cüruf miktarını azaltmaya elverişlidir.Gaz çözünürlüğü, sıvı büzülmesi ve yüksek sıcaklıktaki metal sıvının boşluğun yüzeyinde pişmesi, gözenekler, kum yapışması ve büzülme delikleri gibi kusurları önleyebilir.Bu nedenle, kalıp boşluğunun doldurulmasını sağlamak için daha düşük bir dökme sıcaklığı kullanmaya çalışın.Bir potadan erimiş metalin bir kalıba dökülmesi işlemine dökme denir.Uygun olmayan döküm işlemi, yetersiz döküm, soğuk izolasyon, gözenekler, büzülme delikleri ve cüruf içermesi gibi takım tezgahı döküm kusurlarına ve kişisel yaralanmalara neden olur.
döküm kalitesi
Temel olarak görünüm kalitesi, iç kalite ve kullanım kalitesini içerir.Görünüm kalitesi, dökümün yüzey pürüzlülüğü, yüzey kusurları, boyutsal sapma, şekil sapması ve ağırlık sapması anlamına gelir;iç kalite esas olarak kimyasal bileşim, fiziksel özellikler, mekanik özellikler, metalografik yapı ve delikler, çatlaklar, kalıntılar vb. ile ilgilidir. Ayrışma ve diğer koşullar;hizmet kalitesi, dökümlerin aşınma direnci, korozyon direnci, şok direnci, yorulma, şok emilimi ve diğer özelliklerin yanı sıra işlenebilirlik, kaynaklanabilirlik ve diğer işlem özellikleri dahil olmak üzere farklı koşullar altında çalışma dayanıklılığını ifade eder.
Döküm kalitesinin mekanik ürünlerin performansı üzerinde büyük etkisi vardır.Örneğin, takım tezgahı dökümlerinin aşınma direnci ve boyutsal kararlılığı, takım tezgahının doğruluğunu ve ömrünü doğrudan etkiler;çeşitli pompaların çarklarının, gövdelerinin ve hidrolik parçalarının iç boşluklarının boyutları, doğruluğu ve yüzey pürüzlülüğü pompayı doğrudan etkiler.Hidrolik sistemin çalışma verimliliği, enerji tüketimi ve kavitasyon gelişimi vb.;içten yanmalı motor silindir bloğu, silindir kapağı, silindir gömleği, piston segmanı, egzoz borusu ve diğer dökümlerin soğuğa ve sıcağa karşı dayanıklılığı ve direnci motorun çalışma ömrünü doğrudan etkiler.
Döküm kalitesini etkileyen birçok faktör vardır.Birincisi, dökümlerin tasarım sürecidir.Tasarım yapılırken, çalışma koşullarına ve metal malzeme özelliklerine göre dökümün geometrisi ve boyutunun belirlenmesine ek olarak, tasarımın rasyonelliği, döküm alaşımı ve döküm prosesi özellikleri açısından da dikkate alınmalıdır. boyut etkisi ve katılaşma, büzülme.Kompozisyon ayrışması, dökümlerin deformasyonu ve çatlaması gibi kusurların oluşumunu önlemek veya azaltmak için stres ve diğer problemler.İkincisi, makul bir döküm sürecine sahip olmaktır.Yani, dökümün yapısına, ağırlığına ve boyutuna, döküm alaşımının özelliklerine ve üretim koşullarına göre, uygun ayırma yüzeyini ve modellemeyi, maça yapım yöntemini seçin ve döküm nervürlerini, soğuk demiri, yükselticiyi makul bir şekilde ayarlayın ve kapı sistemi.yüksek kaliteli dökümler sağlamak için.Üçüncüsü, döküm için hammaddelerin kalitesidir.Metal yükü, refrakter malzeme, yakıt, eritici, değiştirici, dökümhane kumu, kalıp kumu bağlayıcısı, kaplama ve diğer malzemelerin kalitesi standartların altında olup, bu da dökümde gözenekler, iğne delikleri, cüruf içerme ve yapışkan kum gibi kusurlara neden olur. dökümün görünüm kalitesini etkileyecektir.ve iç kalite, ciddi durumlarda döküm hurdaya ayrılacaktır.Dördüncüsü süreç operasyonudur.Makul süreç çalışma kurallarının formüle edilmesi, çalışanların teknik düzeyinin iyileştirilmesi ve süreç kurallarının doğru bir şekilde uygulanması gerekmektedir.
Döküm üretiminde, dökümlerin kalitesinin kontrol edilmesi ve denetlenmesi gerekmektedir.Her şeyden önce, hammadde ve yardımcı malzemelerden her bir spesifik ürünün kontrol ve muayenesine kadar süreç kodlarını ve teknik koşulları formüle etmek gerekir.Her süreç, süreç koduna ve teknik koşullara göre sıkı bir şekilde kontrol edilir ve denetlenir.Son olarak, bitmiş dökümlerin kalite kontrolü yapılır.Makul test yöntemleri ve uygun test personeli ile donatılmak.Genel olarak, dökümün görünüm kalitesi için, dökümün yüzey pürüzlülüğü, numune blokları karşılaştırılarak değerlendirilebilir;yüzeydeki ince çatlaklar renklendirme yöntemi ve manyetik toz yöntemi ile kontrol edilebilir.Dökümlerin iç kalitesi, ses frekansı, ultrason, girdap akımı, X-ray ve γ-ray gibi yöntemlerle kontrol edilebilir ve değerlendirilebilir.
Kum dökümlerin kusurları şunlardır: soğuk yalıtım, yetersiz dökme, gözenekler, kum yapışması, kum içerme, kum delikleri ve şişen kum.
1) Yetersiz soğuk izolasyon ve dökme: Sıvı metal doldurma kapasitesi yetersiz veya doldurma koşulları kötü.Boşluk doldurulmadan önce, erimiş metal akışı duracak ve bu da dökümde yetersiz döküme veya soğuk yalıtım kusurlarına neden olacaktır.Döküm yetersiz olduğunda, döküm tam bir şekil elde edemeyecek;soğuk izolasyon sırasında, döküm tam bir şekil alabilse de, tam olarak kaynaşmamış dikişlerin varlığı nedeniyle dökümün mekanik özellikleri ciddi şekilde zarar görür.
Yetersiz dökme ve soğuk izolasyonu önleyin: dökme sıcaklığını ve dökme hızını artırın.
2) Gözeneklilik Gaz, sıvı metal kabuklanmadan önce zamanında kaçmaz ve dökümde delik benzeri kusurlar oluşur.Gözeneklerin iç duvarları pürüzsüz, parlak veya hafif oksitlenmiştir.Dökümde gözenekler oluşturulduktan sonra, etkili taşıma alanı azaltılacak ve dökümün darbe direncini ve yorulma direncini azaltmak için gözeneklerin etrafında stres konsantrasyonu oluşacaktır.Gözenekler ayrıca dökümün kompaktlığını azaltabilir ve hidrostatik test gerektiren bazı dökümlerin hurdaya ayrılmasına neden olabilir.Ayrıca gözeneklilik, dökümün korozyon direncini ve ısı direncini de olumsuz etkiler.
Gözenek oluşumunu önleyin: erimiş metaldeki hava içeriğini azaltın, kum kalıbının hava geçirgenliğini artırın ve boşluğun en yüksek kısmına bir hava yükseltici ekleyin.
3) Yapışkan kum Döküm yüzeyine yapışan çıkarılması zor kum tabakasına yapışkan kum denir.Yapışkan kum sadece dökümlerin görünümünü etkilemekle kalmaz, aynı zamanda döküm temizleme ve kesme iş yükünü arttırır ve hatta makinenin ömrünü etkiler.Örneğin dökülen dişlerin yüzeyinde yapışkan kum olduğu zaman zarar görmesi kolaydır.Pompa veya motor gibi makine parçalarında yapışkan kum varsa akaryakıt, gaz, yağlama yağı ve soğutma suyu gibi akışkanların akışını etkileyerek tüm makineyi lekeleyip yıpratacaktır.
Kumun yapışmasını önleyin: kalıp kumuna toz haline getirilmiş kömür ekleyin ve kalıbın yüzeyine yapışmaz kum boyası uygulayın.
4) Kalın ve büyük yassı dökümlerin ıslak kalıplarla dökümünde kum eklenmesiyle döküm yüzeyinde oluşan oluklar ve yara kusurlarının oluşması çok kolaydır.
Dökümde kum üreten parçaların çoğu kum kalıbın üst yüzeyi ile temas halindedir.Boşluğun üst yüzeyi, kavislenmesi ve bükülmesi kolay olan erimiş metalin radyan ısısından etkilenir.Eğilmiş kum tabakası erimiş metal akışı tarafından sürekli olarak temizlendiğinde Kırılabilir ve parçalanabilir, yerinde kalabilir veya başka yerlere taşınabilir.Dökümün üst yüzeyi ne kadar büyük olursa, kalıp kumunun hacim genişlemesi o kadar büyük ve kum kapanımları oluşturma eğilimi o kadar büyük olur.
5) Kum delikleri, dökümün içinde veya yüzeyinde kalıplama kumu ile doldurulmuş delik benzeri kusurlardır.
6) Genleşme Kumu Döküm sırasında erimiş metalin basıncı altında kalıp duvarının hareket etmesi nedeniyle dökümün lokal genleşmesiyle oluşan bir kusurdur.Kum genleşmesini önlemek için, kum kalıbının mukavemeti, kum kutusunun sertliği, kutuyu kapatırken basınç kutusu kuvveti veya sıkma kuvveti arttırılmalı ve yüzeyini yapmak için dökme sıcaklığı uygun şekilde düşürülmelidir. erimiş metalin kalıp üzerindeki etkisini azaltmak için erimiş metal kabuğu daha erken.baskı yapmak.
Kalite Kontrol
döküm
Dökümlerin muayenesi temel olarak boyutsal muayene, görünüm ve yüzeyin görsel muayenesi, kimyasal bileşim analizi ve mekanik özellik testini içerir.Döküm işleminde daha önemli veya problemlere eğilimli dökümler için, sfero dökümlerde kullanılabilen tahribatsız muayene de gereklidir.Kalite testi için tahribatsız test teknikleri, sıvı penetrant testi, manyetik parçacık testi, girdap akımı testi, radyografik test, ultrasonik test ve titreşim testini içerir.
1. Döküm yüzeyi ve yüzeye yakın kusurların tespiti
1) Sıvı Penetrasyon Testi
Sıvı penetran testi, yüzey çatlakları, yüzey iğne delikleri ve çıplak gözle bulunması zor olan diğer kusurlar gibi dökümlerin yüzeyindeki çeşitli açılma kusurlarını incelemek için kullanılır.Yaygın olarak kullanılan penetran muayenesi, yüksek penetranlığa sahip renkli (genellikle kırmızı) bir sıvıyı (penetrant) ıslatmak veya püskürtmek için olan renklendirme muayenesidir ve penetran, açıklık kusuruna nüfuz eder ve yüzey penetranını hızla siler. .katman ve ardından dökümün yüzeyine kuruması kolay bir görüntüleme maddesi (geliştirici olarak da adlandırılır) püskürtün.Açılma kusurunda kalan penetran emildikten sonra kusurun şeklini, boyutunu ve dağılımını yansıtabilecek teşhir maddesi boyanır.Test edilen malzemenin yüzey pürüzlülüğünün artmasıyla penetrasyon testinin doğruluğunun azaldığı, yani yüzey ne kadar parlaksa algılama etkisinin o kadar iyi olduğu belirtilmelidir.Renk tespitinin yanı sıra floresan penetrant tespiti de yaygın olarak kullanılan bir sıvı penetran tespiti yöntemidir.Işınlama gözlemi için ultraviyole ışıkla donatılması gerekir ve algılama hassasiyeti, renklenme algılamasından daha yüksektir.
2) Girdap akımı testi
Girdap akımı testi, genellikle 6-7 MM'den daha derin olmayan yüzeyin altındaki kusurları incelemek için uygundur.Girdap akımı testi iki türe ayrılır: yerleştirilmiş bobin yöntemi ve geçiş tipi bobin yöntemi.Test parçası, alternatif akım akarken bobinin yanına yerleştirildiğinde, test parçasına giren alternatif manyetik alan, test parçasında uyarma manyetik alanına dik yönde akan bir girdap akımı (girdap akımı) ve girdap akımını indükleyebilir. Bobin içindeki orijinal manyetik alan kısmen azaltılarak, bobin empedansının değişmesine neden olacak şekilde, uyarma manyetik alanına zıt bir manyetik alan oluşturulur.Döküm yüzeyinde bir kusur varsa, girdap akımının elektriksel özellikleri bozulacak ve kusurun varlığı tespit edilecektir.Girdap akımı incelemesinin ana dezavantajı, tespit edilen kusurun boyutunun ve şeklinin görsel olarak görüntülenememesidir.Genellikle kusurun sadece yüzey konumu ve derinliği belirlenebilir., ve iş parçası yüzeyindeki küçük açık kusurları tespit etmek için penetran tespiti kadar hassas değildir.
3) Manyetik parçacık muayenesi
Manyetik parçacık muayenesi, yüzey kusurlarını ve yüzeyin birkaç milimetre derinliğindeki kusurları tespit etmek için uygundur.Kontrol işlemleri için DC (veya AC) manyetizasyon ekipmanı ve manyetik toz (veya manyetik süspansiyon) gerektirir.Mıknatıslama ekipmanı, dökümün iç ve dış yüzeylerinde bir manyetik alan oluşturmak için kullanılır ve kusurları ortaya çıkarmak için manyetik toz veya manyetik süspansiyon kullanılır.Dökümün belirli bir aralığında bir manyetik alan oluşturulduğunda, manyetize alandaki kusurlar bir kaçak manyetik alan oluşturacaktır.Manyetik toz veya süspansiyon serpildiğinde, kusurların görüntülenebilmesi için manyetik toz çekilir.Bu şekilde görüntülenen kusurlar temel olarak manyetik alan çizgilerine çapraz olan kusurlardır ve manyetik alan çizgilerine paralel uzun şekilli kusurlar görüntülenemez.Bu nedenle, bilinmeyen bir yöndeki her bir kusurun tespit edilebilmesi için çalışma sırasında manyetizasyon yönünün sürekli olarak değiştirilmesi gerekir..
2. Dökümlerin iç kusurlarının tespiti
Dahili kusurlar için yaygın olarak kullanılan tahribatsız muayene yöntemleri radyografik muayene ve ultrasonik muayenedir.Bunlar arasında, radyografik muayene etkisi en iyisidir, dahili kusurların tipini, şeklini, boyutunu ve dağılımını yansıtan sezgisel bir görüntü elde edebilir, ancak büyük kalınlıktaki büyük dökümler için ultrasonik muayene çok etkilidir ve dahili kusurların konumu daha doğru bir şekilde ölçülebilir., eşdeğer boyut ve dağılım.
1) Radyografik inceleme (Mikro odaklı XRAY)
X-ışınları veya γ-ışınları genellikle ışın denetimi için radyasyon kaynağı olarak kullanılır, bu nedenle ışın üretmek için ekipman ve diğer yardımcı tesisler gereklidir.İş parçası ışın alanına yerleştirildiğinde, ışının radyasyon yoğunluğu dökümün iç kusurlarından etkilenecektir.Döküm yoluyla yayılan radyasyon yoğunluğu, kusurun boyutuna ve doğasına göre yerel olarak değişir ve kusurun bir radyografik görüntüsünü oluşturur; bu, bir radyografik film aracılığıyla görüntülenen ve kaydedilen veya bir floresan ekran aracılığıyla gerçek zamanlı olarak saptanan ve gözlemlenen veya saptanan kusurun radyografik görüntüsünü oluşturur. bir radyasyon sayacı ile.Bunlar arasında radyografik film ile görüntüleme ve kayıt yöntemi en sık kullanılan yöntemdir ve yaygın olarak radyografik muayene olarak adlandırılır.Radyografi ile yansıtılan kusur görüntüsü sezgiseldir ve kusurların şekli, boyutu, sayısı, düzlem konumu ve dağılım aralığı hepsi gösterilebilir, ancak kusurun derinliği genel olarak yansıtılamaz ve özel ölçü ve hesaplamalara ihtiyaç vardır. belirlemek için.Uluslararası döküm endüstrisi ağı, pahalı ekipman ve yüksek kullanım maliyeti nedeniyle yaygınlaştırılamayan ışın bilgisayarlı tomografi yöntemini uygulamıştır, ancak bu yeni teknoloji, yüksek çözünürlüklü ışın algılama teknolojisinin gelecekteki gelişim yönünü temsil etmektedir.Ek olarak, bir nokta kaynağına yaklaşan bir mikro odaklı X-ray sisteminin kullanılması, daha büyük odak cihazlarının yarattığı bulanık kenarları ortadan kaldırarak daha keskin görüntü anahatları sağlar.Dijital bir görüntüleme sistemi kullanmak, görüntünün sinyal-gürültü oranını iyileştirebilir ve görüntünün netliğini daha da iyileştirebilir.
2) Ultrasonik test
Ultrasonik testler, dahili kusurları incelemek için de kullanılabilir.İç yüzeye çarptıklarında yansımalar oluşturmak veya kusurları bulmak için kusurları oluşturmak için ses ışınlarının döküm içinde yüksek frekanslı ses enerjisiyle yayılmasını kullanır.Yansıtılan akustik enerjinin büyüklüğü, iç yüzeyin veya kusurun yönlülüğünün ve doğasının ve böyle bir reflektörün akustik empedansının bir fonksiyonudur, bu nedenle çeşitli kusurlardan veya iç yüzeylerden yansıyan akustik enerji, kusurların varlığını tespit etmek için uygulanabilir. , duvar kalınlığı veya kusurun yüzey derinliği.Yaygın olarak kullanılan bir tahribatsız muayene yöntemi olarak ultrasonik testin başlıca avantajları şunlardır: küçük çatlakları tespit edebilen yüksek algılama hassasiyeti;kalın kesitli dökümleri tespit edebilen büyük penetrasyon kabiliyeti.Başlıca sınırlamaları şunlardır: karmaşık kontur boyutları ve zayıf yönlülük ile süreksiz kusurlar için yansıma dalga biçimlerini yorumlamak zordur;tane boyutu, mikro yapı, gözeneklilik, inklüzyon içeriği veya ince dağılım Çökeltiler vb. gibi istenmeyen iç yapılar için ayrıca dalga biçimi yorumunu da engeller;ek olarak, algılama için referans işaretleri gereklidir
Kayıp Balmumu Yatırım Döküm Parçaları Hassas Çelik Döküm Parçaları özel metal damgalama
Döküm kusurları nasıl onarılır:
Dökümlerin büzülme kusurunu gidermeye yönelik yöntemin en temel odak noktası “termal denge”dir.Yöntem:
(1) Takım tezgahı döküm yapısının oluşturduğu kalın parçalarda ve sıcak bağlantılarda hızlı katılaşma uygulanır, bu da takım tezgahı dökümlerinin sıcaklık alanının temel dengesine yapay olarak neden olur.İç ve dış soğuk demir kullanılmaktadır ve lokal olarak zirkon kumu, kromit kumu veya büyük ısı depolu özel kaplamalar kullanılmaktadır.
(2) Makul süreç tasarımı.İç kızak, sık ve dağınık olan takım tezgahı dökümünün karşı duvarında bulunur.Kalın duvarlı parçaya ilk giren erimiş metal önce katılaştırılır ve ince duvarlı parça daha sonra katılaştırılır, böylece tek tip katılaşma temelde her yerde sağlanır.Tek tip duvar kalınlığına sahip takım tezgahı dökümleri için birden fazla kanal ve havalandırma kullanın.Genel ısının dengelenmesi için dağılmış ve eşit olarak dağıtılmış birçok iç koşucu vardır.Hava çıkışı ince ve çoktur, yani egzoz engellenmez ve ısı dağıtılır.
(3) İç koşucunun konumunu değiştirin
(4) Büyük ısı depolamalı modelleme malzemelerinin seçimi, köpük kaybı olan aşınma önleyici ürünlerin üretimi için son derece önemlidir!Kromit kumu, kuvars kumu ve diğer kum türlerini düşük ısı depolama ile değiştirir, bu da iyi sonuçlar elde eder ve mikro sismik döküldükten sonra daha iyidir!
(5) Düşük sıcaklık ve hızlı yanan, açık döküm sistemi.Erimiş metalin kalıbı hızlı, düzgün ve eşit bir şekilde doldurmasını sağlayın.Bu duruma bağlıdır.
(6) Sfero döküm takım tezgahı, yüksek mukavemete, ≧ 90 yüzey sertliğine ve büzülme gözenekliliğini ortadan kaldırmak için faydalı olan kum kutusunun yüksek sertliğine sahiptir.
(7) Yükseltici gerektiğinde, önce ısıtıcıyı hareket ettirin ve ısıtma bölümünden çıkın.Yükseltici sıcak bölüme yerleştirilirse, yükselticinin boyutu "ısı üzerinde ısıtma" oluşturacak şekilde büyütülür.İyi yapılmazsa, yalnızca büzülme gözenekliliğinin giderilmesi zor olmakla kalmaz, aynı zamanda konsantre büzülme boşlukları da oluşacak ve bu da işlem verimini azaltacaktır.
(8) Döküm kalıbının eğimli yerleştirilmesi ve alaşımlanması faydalıdır.Takım tezgahı dökümlerinin büzülme kusurlarını ortadan kaldırmak, karmaşık bir anlama ve uygulama sürecidir."Isı dengesi" temel prensibinden hareketle, ju gövde dökümlerinin bilimsel analizi yapılmalı, makul bir proses planı oluşturulmalı, uygun kalıplama malzemeleri, takımlar ve doğru operasyon seçilmeli ve standardize edilmelidir.Daha sonra takım tezgahı dökümlerinin herhangi bir büzülme kusuru çözülebilir.
Çeşitli faktörlerden dolayı gözenekler, iğne delikleri, cüruf kalıntıları, çatlaklar ve çukurlar gibi kusurlar sıklıkla ortaya çıkar.Yaygın olarak kullanılan tamir ekipmanları argon ark kaynak makinesi, direnç kaynak makinesi, soğuk kaynak makinesi vb. Yüksek kalite ve görünüm gerektirmeyen döküm kusurları, argon ark kaynak makineleri gibi yüksek ısı üretimi ve yüksek hıza sahip kaynak makineleri ile tamir edilebilir.Bununla birlikte, hassas döküm kusurlarının onarımı alanında, argon kaynağı ısısının büyük etkisi nedeniyle onarım, döküm deformasyonuna, sertlik azalmasına, kabarcıklara, yerel tavlamaya, çatlamaya, iğne deliklerine, aşınmaya, çiziklere, alttan kesiklere veya yetersiz yapıştırma kuvvetine neden olacaktır. ve stres hasarı gibi dahili ikincil kusurlar.Soğuk kaynak makinesi sadece yukarıdaki eksikliklerin üstesinden gelir ve avantajları esas olarak ısıdan etkilenen küçük alana yansır, dökümün önceden ısıtılması gerekmez ve oda sıcaklığında soğuk kaynak onarımı, bu nedenle deformasyon, alttan kesme ve kalıntı yoktur. stres, yerel tavlama yok ve döküm metalinde değişiklik yok.kuruluş durumu.Bu nedenle, soğuk kaynak makinesi, hassas dökümlerin yüzey kusurlarının onarımı için uygundur.Soğuk kaynağın onarım aralığı, tekrarlanan eritme ve Φ1.5-Φ1.2mm'lik kaynak onarım noktalarının birikmesi işlemidir.Geniş alan kusurlarını onarma sürecinde, onarım verimliliği, yaygın uygulamasını kısıtlayan tek faktördür.Büyük kusurlar için, geleneksel kaynak onarım işlemi ve döküm kusuru onarım makinesinin birlikte uygulanması önerilir.Ama bazen çok fazla kusurumuz olmuyor, bu yüzden çok fazla para yatırmamıza gerek yok.Kullanışlı ve basit olan bazı tamir maddeleriyle tamir edebiliriz.Örneğin, demir malzemeleri onarmak için (Jinsucheng) JS902 kullanabiliriz.Tükenmezse daha sonra kullanılabilir, bu da üreticilerimiz için maliyet tasarrufu sağlayabilir, dökümhanelerimizin ürünlerin kalitesini iyileştirmek için daha fazla para yatırmasına izin verebilir ve kullanıcıların daha fazla zenginlik yaratmasına izin verebilir.
3. Döküm kalite kontrol sonuçları
Döküm kalite kontrol sonuçları genellikle üç kategoriye ayrılır: nitelikli ürünler, onarılan ürünler ve reddedilen ürünler.
1) Nitelikli ürünler, görünüm kalitesi ve iç kalitesi, teslimat kabulü için ilgili standartları veya teknik koşulları karşılayan dökümleri ifade eder;
2) Yeniden işlenmiş ürünler, görünüm kalitesi ve iç kalitesi standartları ve kabul koşullarını tam olarak karşılamayan ancak onarılmasına izin verilen ve onarımlardan sonra standartları ve döküm teslim kabul teknik gerekliliklerini karşılayabilen dökümleri ifade eder;
3) Hurda, görünüm kalitesi ve iç kalite açısından niteliksiz olan ve onarılmasına izin verilmeyen veya onarımdan sonra döküm teslimi kabulü için standartları ve teknik gereksinimleri karşılamayan hala dökümleri ifade eder.Atık ayrıca iç atık ve dış atık olarak ikiye ayrılır.Dahili atık, dökümhanelerde veya dökümhanelerde bulunan atık dökümleri ifade eder;dış atık, döküm teslim edildikten sonra bulunan atık anlamına gelir ve bunun neden olduğu ekonomik kayıp, iç atıklardan çok daha fazladır.[2]
Dökümlerin Katılaşma Modunu Etkileyen Faktörler
Dökümlerin katılaştırılması için birçok yöntem vardır.Dökümün katılaşma işlemi sırasında, bölüm genellikle üç bölgeye ayrılır: 1-katı faz bölgesi 2-katılaşma bölgesi 3-sıvı faz bölgesi, katılaşma bölgesi üzerinde daha büyük bir etkiye sahiptir, katılaşma bölgesinin genişliğidir ve katılaşma Yöntem buna göre bölünür.İlk olarak, ara katılaşma: çoğu alaşımın katılaşması, katman katman katılaştırma ile macun katılaşması arasındadır.İkincisi, katman katman katılaşma: saf metal, ötektik bileşim alaşımlarının katılaşma sırasında katılaşma bölgesi yoktur ve sıvı ve katı iki faz bir sınırla açıkça ayrılır.Merkeze doğrudan erişim.Üçüncüsü, duygusal katılaşma: alaşımın kristalleşme sıcaklık aralığı çok geniştir.Belirli bir katılaşma periyodu sırasında, döküm yüzeyinde katı bir tabaka yoktur ve katılaşma bölgesi tüm kesit boyunca ilerler, önce yumuşak ve sonra katılaşır.İlgili uzmanlar, dökümlerin katılaşma modunu etkileyen faktörlerin özetlendiğini söyledi: Birincisi, dökümlerin sıcaklık gradyanı.Alaşımın kristalleşme sıcaklık aralığı sabit olduğunda, katılaşma bölgesinin genişliği, dökümün iç ve dış katmanlarının sıcaklık gradyanına bağlıdır.Sıcaklık gradyanı ne kadar küçük olursa, katılaşma bölgesi o kadar geniş olur.(İç ve dış arasındaki sıcaklık farkı büyüktür, soğutma hızlıdır ve katılaşma bölgesi dardır).İkincisi, alaşımın kristalleşme sıcaklık aralığı.Küçük aralık: Katılaşma bölgesi dardır ve katman katman katılaşma eğilimi gösterir.Örneğin: kum dökümü, düşük karbonlu çelik katılaşma katman katman, yüksek karbonlu çelik macun katılaşması.
Döküm kusuru tamir maddesi, iki bileşenli, çimento benzeri, oda sıcaklığında kürlenen polimer reçine tutkalı, takviye dolgu maddesi olarak metal ve alaşımlı polimer metal kompozit soğuk kaynak onarım malzemesidir.Metal ile yüksek yapışma mukavemetine sahiptir ve temelde aynı rengi koruyabilir ve aşınma direnci, korozyon direnci ve yaşlanma direnci özelliklerine sahiptir.Kürlenmiş malzeme yüksek mukavemete sahiptir, büzülme yapmaz ve çeşitli makine türleri ile işlenebilir.Aşınma direnci, yağ direnci, su direnci ve çeşitli kimyasal korozyon direnci gibi mükemmel özelliklere sahiptir ve 120 ° C'lik yüksek sıcaklığa dayanabilir.
kullanmak
Döküm kusuru tamir maddesi, çeşitli alaşım malzemeleri ve modifiye edilmiş sertleştirilmiş ısıya dayanıklı reçinelerin birleştirilmesiyle elde edilen yüksek performanslı polimerik bir metal malzemedir.Çeşitli metal dökümlerin ve 2 mm'den büyük kusurlu çeşitli dökümlerin onarımı için uygundur., çatlak, aşınma, korozyon onarımı ve yapıştırma.Genellikle daha az katı renk gereksinimleri ile çeşitli döküm kusurlarının onarımı için kullanılır.Yüksek mukavemete sahiptir ve ana malzeme ile işlenebilir.
nasıl tespit edilir
Dökümün özellikleri, işleme kalitesini doğrudan etkiler ve sertlik değeri, dökümün işlenmesini belirlemek için önemli bir göstergedir.
1) Brinell sertliği: Esas olarak dökümlerin, dövme parçaların, demir dışı metal parçaların, sıcak haddelenmiş kütüklerin ve tavlanmış parçaların sertliğini ölçmek için kullanılır.Ölçüm aralığı ≯HB450'dir.
2) Rockwell sertliği: HRA, esas olarak, malzemelerin sertliğini ve semente karbür, nitrürlenmiş çelik vb. gibi HRC67'nin üzerindeki yüzey sertliğini ölçmek için yüksek sertlikteki test parçaları için kullanılır, ölçüm aralığı HRA>70'dir.HRC esas olarak çelik parçaların (karbon çeliği, takım çeliği, alaşımlı çelik vb.) su verme veya temperlemeden sonra sertlik ölçümü için kullanılır ve ölçüm aralığı HRC20~67'dir.
3) Vickers sertliği: İnce parçaların ve çelik levha parçaların sertliğini ölçmek için kullanılır ve ayrıca karbonlama, siyanürleme ve nitrürleme gibi yüzey sertleştirilmiş parçaların sertliğini ölçmek için de kullanılabilir.
Ana Test ve Muayene Cihazı
Numara. | Cihaz | Tip | miktar | Durum | Not |
1 | Son söndürme makinesi | DZJ-I | 1 | Çalışma | Test yapmak |
2 | Elektrik dirençli fırın | SX2-8-12 | 2 | Çalışma | Test yapmak |
3 | Ters metalurjik mikroskop | 4XCE | 1 | Çalışma | Denetleme |
4 | Yüksek sıcaklık kutusu dirençli fırın | SX2-4-13 | 1 | Çalışma | Test yapmak |
5 | Otomatik dijital ekran Rockwell test cihazı | 200HRS-180 | 1 | Çalışma | Denetleme |
6 | Elektronik Brinell sertlik test cihazı | THB-3000 | 1 | Çalışma | Denetleme |
7 | HR-150B Rockwell sertlik test cihazı | HR-150B | 1 | Çalışma | Denetleme |
8 | Hızlı çok elemanlı analizör | JS-DN328 | 1 | Çalışma | Denetleme |
9 | Elektrik ark ocağı | JSDL-8 | 1 | Çalışma | Test yapmak |
10 | Hızlı çok elemanlı analizör(C & S) | JS-DN328 | 1 | Çalışma | Denetleme |
11 | Kızılötesi termometre | AR872 | 2 | Çalışma | Denetleme |
12 | Taşınabilir kimyasal bileşim analizörü | AR872 | 2 | Çalışma | Denetleme |
13 | Test numunesi örnekleyici | KW30-6 | 1 | Çalışma | Denetleme |